To ensure successful welding of dissimilar metals, it’s important to partner with only highly experienced, expert welding fabricators. Typically, when customers venture outside the realm of standard materials, costs increase exponentially. And since specialty materials can’t be bought off the shelf, the lead time for replacement parts and fittings is usually prolonged as well. All of these factors limit the wiggle room welders have for trial and error.
Frequently, we are called upon when existing OEM equipment has original dissimilar metals that were not joined properly. In these situations, our team will repair an existing weld or add a new component to a piece of equipment.
Key Considerations in Dissimilar Metal Welding
Even if a fabricator has previously welded one of the two dissimilar metals, this experience won’t necessarily translate to a successful dissimilar weld. Welders often need to implement completely different techniques to accommodate both types of metal. To determine the proper techniques, the physical properties of the base material and the working conditions of the completed piece must first be determined.
Material Considerations
Depending on the application, dissimilar metal joining processes can be extremely easy or incredibly difficult. Fabricators must consider important physical properties of each base material, including:
- Hardness
- Ductility
- Malleability
- Tensile strength
- Density
- Melting temperatures of each metal
- Thermal conductivity of each metal
- Weldability
- Whether the metals need to be preheated prior to welding
The fabricator needs this information to determine the proper filler metal for welding the dissimilar metals. A filler material must be selected that is as close a match as possible to the weaker of the two metals; this will prevent it from weakening any further and allows the two material being joined to shrink at different rates without causing cracking in the weld, thereby forming a stronger bond at the fusion point.
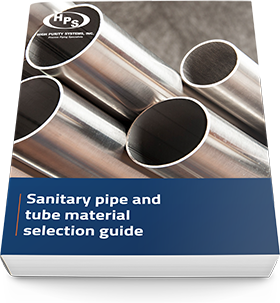
Sanitary pipe and tube material selection guide
See how matching materials to processes boosts performance and increases safety in your operations.
Working Environment Considerations
Prior to welding, key considerations for the working environment of the final part should include:
- Temperatures
- Chemicals
- Environment
- Highly abrasive?
- Will there be force on the welded joint?
Selecting a method and process
Depending on the application and the strength of the materials being joined, the best welding method for the job can vary — from soldering and brazing to GTAW, SMAW, or GMAW. After the weld is complete, the material composition of the two different metals, as well as the application of the final part, will determine whether or not the welded components must be stress relieved. Certain materials or use cases require post weld heat treatment to get the metals back to their original state of strength.
Selecting the right fabricator
When selecting a fabricator for joining different types of metal, customers should be prepared to ask prospective partners about their experience with these types of jobs. Ask the weld shop to provide specific examples of past dissimilar welding projects. The right organization will have a team of certified welders who understand your application and can provide references for similar applications.
Success with HPS
HPS has proudly completed numerous high-stakes dissimilar welding projects, including joining stainless steel to Inconel, copper, aluminum, and carbon steel. Our team can efficiently tackle each unique job to meet tight deadlines.
To learn more about how HPS can help you get started with your next dissimilar welding project, contact us today!
Contact High Purity Systems
Have a question about a piping challenge? Want to discuss an upcoming project? Let’s talk.