The Challenge
The High Purity Systems (HPS) team was excited for the opportunity to reach for the stars when we were contracted to build fourteen stainless process piping skids for ground support equipment for an unmanned rocket resupply mission to the International Space Station (ISS). Designed collaboratively by a team of engineers who were working directly with our client in Dulles, VA, these skids were integral to the process piping system supporting a Liquid Fueling Facility (LFF) for the NASA launch facility at Wallops Island, Virginia.
The need for a fueling station arose when NASA began subcontracting their supply deliveries to the ISS. After visiting our fabrication facility in Northern Virginia, it became clear to the engineers working on the LFF project that HPS was the best company to build the process piping skids. As the first of its kind on the East Coast, we are proud to be part of the team that built the infrastructure of the Liquid Fueling Facility at Wallops Island.
The Strategy
We designed the facility skids with job specific components and precise specifications to operate in severe weather and operational conditions in adherence with the critical guidelines set up for the LFF program. Once the final drawings were approved for fabrication, the HPS team commenced production.
We built the skids (some as big as 8’ wide by 22’ long) with structural steel and then they were hot dip galvanized to ensure maximum corrosion resistance. To cut down on conductive electrolysis, we machined and installed micarta laminate sheets as standoffs between the steel supports and the stainless steel piping.
After we removed all possibilities for stainless steel to come in contact with the galvanized steel, we began the piping work. We laid out all the skids in order of schedule priority at our fabrication facility; this made the entire construction and fabrication process as efficient as possible.
The crews had to pay close attention to detail to adhere to welding codes ASME B31.1, as well as severe cyclic criteria for ASME B31.3 process piping. We took extreme care to guarantee that each weld would perform reliably for the life of the system. The project utilized equipment including TIG welders, tube and pipe flaring equipment, and our mandrel pipe bender. By bending the stainless steel pipe, we were able to increase productivity and reduce overall costs of the project.
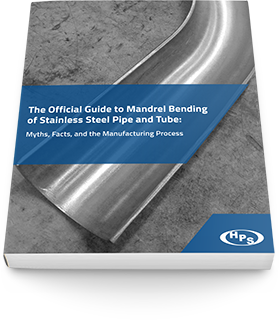
The official guide to mandrel bending
Separate facts from myths and save up to 50% on project costs compared to cutting and welding.
Because of the one-of-a-kind nature of this project, engineering modifications were ongoing throughout production. With frequent conversations between HPS and the designer to keep communication open and respond to any challenges before they became problematic, everyone worked together smoothly in an effort to produce the best product with the least amount of down time.
Each skid had an inlet and an outlet, with some equipped with more than one. From the inlet flange, the stainless steel pipe system meandered through a series of valves, regulators, and flow meters to meet the outlet flange. Planted over top of the main piping was a system of hangers for more tubing. The ¼” and ½” tubing was bent, flared, routed, and rose together before splitting off to go to its final connection point.
We used some of the tubing to pipe out pneumatic controllers on valves and other tubing to supply pressure to gauges and flow-indicators. Each skid was a cleanly-designed, efficient stainless maze. Once we finished the piping, the electricians mounted switch boxes and finally installed safety shut-offs and indicator lights.
The Result
Thanks to a team effort from engineers, designers, welders and fabricators, the creation of these LFF skids resulted in a successful rocket launch in February 2013. We were truly proud to be part of the ground support effort for this project. With the quality systems that we supplied for this launch pad, HPS was able to reach for the stars — and beyond.
Contact High Purity Systems
Have a question about a piping challenge? Want to discuss an upcoming project? Let’s talk.