The Opportunity
Our team was excited to have an out-of-this-world opportunity to build ground support infrastructure at a NASA rocket launch pad, located at Wallops Island, VA, for a new liquid fueling facility (LFF) to support an unmanned rocket resupply mission to the International Space Station (ISS).
High Purity Systems (HPS) has over 30 years of experience with a broad range of projects, but some of our proudest moments have come from critical use installations just like this — where the stakes are high, and the job requires perfect precision.
Our client, an aerospace general contractor, teamed with HPS for the installation of the tank storage area piping and the pad area piping for the launch pad. These stainless steel piping systems included rocket fuel piping, liquid oxygen (LO2) piping, liquid nitrogen (LN2) piping and gaseous helium (He) and nitrogen (N2) piping.
HPS was very excited about this on-site piping installation opportunity because part of the scope included the connection of fourteen stainless process piping control skids that were previously awarded to HPS in the months prior to the on-site project. These skids were welded and assembled at our fabrication facility in Manassas, VA. There’s nothing more satisfying than installing equipment that we built!
The Strategy
The site conditions for installation were quite challenging, to say the least – the project duration was 30 months, and it all happened on an island only a few yards away from the Atlantic Ocean. The constant wind, cold, heat, sand, mosquitoes, snowstorms, an earthquake, and even a hurricane all posed challenges! All this while tasked with producing 100% x-ray quality welds through NDT radiographic inspection and providing full NASA required documentation to support outer-orbit travel.
In addition to the challenging working conditions, due to the one-of-a-kind nature of this job, we had to be flexible in making engineering modifications throughout the entire project. Our team regularly met with the designers and NASA engineers to ensure that we were all on the same page about producing and installing the best product with the smallest amount of impact to the launch facility schedule.
All project materials were required to be purchased under the Buy American Act. Valves and components had long lead times, some up to 36 weeks, so proper planning and scheduling were a must.
HPS is always on the lookout for opportunities to improve the schedule while reducing costs. Mandrel bending the stainless piping, instead of welding, was an excellent way to accomplish this. By utilizing our mandrel bending equipment in our Manassas VA fabrication facility, we were able to remotely support the on-site installation and ensure that we weren’t impacted by the various site conditions we encountered at the launch pad.
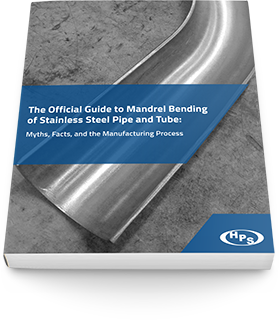
The official guide to mandrel bending
Separate facts from myths and save up to 50% on project costs compared to cutting and welding.
Our skilled team of project managers, welders and steamfitters collaborated to install various systems using a combination of TIG welded, and mandrel bent stainless steel piping from ½” through 12” ranging from schedule 10 to schedule XXH (Double Extra Heavy) wall thickness. Our team also flared tubing to connect AN 37 degree JIC fittings that were used in the control systems.
The on-site piping installation exceeded every specification for cleanliness and critical use required for this high stakes project. These standards included ASME B31.1, ASME B31.3 for severe cyclic conditions, NASA specifications and documentation, and IEST-STD-CC1246D cleanliness specifications. Expert TIG welders who had extensive training and experience performed the B31.3 severe cyclic welds.
The Result
By the end of the project, each system was a magnificent and complex network of stainless steel. We are proud that HPS’ on-site process piping installation was a critical part of this project.
Our careful execution helped NASA to reach for the stars and beyond with a successful rocket launch in February 2013!
Contact High Purity Systems
Have a question about a piping challenge? Want to discuss an upcoming project? Let’s talk.