Whether your project requires TIG (Manual GTAW), fusion orbital welding (Automatic GTAW), wire feed orbital (Semi-Automatic GTAW), stick (SMAW), or MIG welding (GMAW), we are the experts in precision welding solutions.
All of our welders are certified to Section IX of the ASME Boiler and Pressure Vessel Code (B&PV), continually meeting and exceeding a wide array of welding standards. We are well-versed in welding similar and dissimilar metals, both at our fabrication facility and on your project site. We utilize third party welding inspectors.
At HPS, we weld more than just pipe and tube. Many of our customers have called upon us to weld together unique and custom assemblies that range from stainless steel to exotic metal.
Our team excels at producing standard as well as complex pipe and tube spool configurations. From extremely small connections with challenging weld angles, to large spools that require our extensive knowledge to overcome material deformation from the various weld locations. We’ve been asked to do it all, and delivered every time.
We regularly provide orbital welding services to produce extremely intricate skidded systems for use in the aerospace, chemical, agriculture, and oil and gas industries. We fabricated and delivered 14 ground support equipment stainless steel skids to the NASA Wallops Island Flight Facility in support of the ongoing satellite and International Space Station support missions where we then installed the ground support skids and the interconnecting piping onsite. These unique welding challenges and required level of precision and detail are where the HPS team’s expertise shines.
Contact High Purity Systems
Have a question about a piping challenge? Want to discuss an upcoming project? Let’s talk.
The High Purity Systems team has developed 7 patents that give the welder and the weld inspector tools to enhance the overall quality of the welded system.
These patented tools include: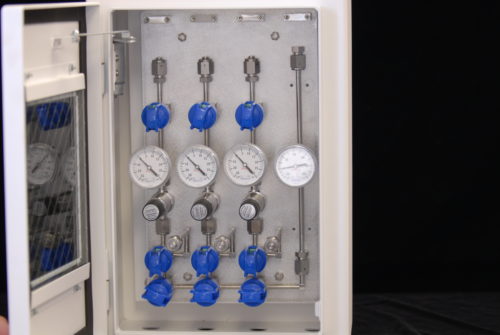
- A back purge instrument that closely monitors and regulates the ID inert gas purge pressure during welding to create the most consistent and repeatable weld no matter how small the diameter.
- A “Go/No-Go” weld profile tool that removes interpretation of the welding specification and gives the welder and the weld inspector a tool to measure to the final weld parameters per the actual welding spec. Many times we’ve encountered situations where the welder and the inspector each interpret the orbital welding requirements differently. This weld profile tool is a game-changer for taking individual interpretation out of weld inspections!
These proprietary tools are put to use daily in our certified Class 100/Class 1000 Clean Room where we specialize in producing welded solutions for the semiconductor, aerospace, and biopharmaceutical industries. Our in-house clean room allows us to offer the double bagging services required for the most stringent clean room welding applications our customers require. We also have extensive experience in delivering comprehensive weld documentation packages for FDA required validation/turnover packages and NASA required documentation for aerospace projects.
Whether you need to orbital weld a 1/16” OD tube or MIG weld a 42” diameter pipe for a waste water treatment plant, the High Purity Systems team is ready to review your CAD drawing or prints and get to work on your one-off prototype or high volume production run. Don’t have a drawing? No problem, we can assist with that too. See samples of our work here and review our complete list of welding capabilities below.
Other Information:
- Orbital Pipe Welding
- Orbital Tube Welding
- Orbital Welding Equipment
- Orbital Welding Systems
- Orbital Welding Process
- Orbital Welding Applications
Specifications
General Welding Capabilities
- High Purity Welding
- Clean Room Welding
- Sanitary Welding
- Hygienic Welding
- Spool Fabrication
- Contract Welding
- Production Welding
- Small Parts Welding
- ASME Stamp Ready
Welding Processes
- Orbital Welding
- TIG Welding
- GTAW (Gas Tungsten Arc Welding)
- MIG Welding
- GMAW (Gas Metal Arc Welding)
- Stick Welding
- SMAW (Shielded Metal Arc Welding)
- Silver Soldering
- Brazing (Medical Gas and High Purity)
- Seam Welding
- Spot Welding
- Spray Welding
- Stud Welding
- Plastic Welding, including:
- Socket Fusion
- IR Butt Fusion
- Bead & Crevis Free (BCF)
- Smooth Inner Bore (SIB)
- Hot Air Welding
Welding Specializations
- Holder of 8 patents that enhance quality of orbital welding
- Proprietary system that closely regulates purge pressure to make the weld more consistent at small diameters
- Small Diameter Tube Welding
- Utility Panels
- Skidded System Fabrication
- Pure argon environment to reduce oxidation
- Clean Room Class 100 / Class 1000
Welding Operations
- Automated
- Semi-Automated
- Free Hand
- Clean Room Class 100 / Class 1000
- Plastics - Free Hand for the manual welding and computer controlled for the IR, BCF and SIB machines
Materials
- Aluminum
- Cast Iron
- Copper
- Exotic Metals
- Hastelloy®
- Inconel®
- Molybdenum
- Monel®
- Tungsten
- Nickel
- Stainless Steel
- AL6XN Duplex Stainless Steel
- Titanium
- Magnesium
- Plastics, including:
- Polypropylene
- PVDF
- CPVC
- PVC
- Polyurethane
- HDPE
- and various other plastics
Minimum Outside Diameter (Min OD)
1/16” Stainless Steel Tubing
Maximum Outside Diameter (Max OD)
42" (hand or MIG welding)
Production Volume
- Prototypes
- Specialty Production Runs
- Low Volume
- High Volume
- Emergency Production Runs
- Emergency Repairs
Typical Lead Time
From SAME DAY based on customer need and project complexity
Welding Certifications
All welders certified to Section IX of the ASME Boiler and Pressure Vessel Code
Weld Testing
Per ASME Section V of the Boiler and Pressure Vessel Code
Weld Quality Control
- In-house Welding Inspectors
- ACCP Level 2
- AWS QC1
- 3rd party CWI available as required on field installations
- 3rd party Radiographic testing (x-ray) to any B31.1, B31.3 or other ASME standard
- Magnaflux Magnetic particle inspection
- Dye penetrant testing
- UT ultrasonic testing
Standard Biopharmaceutical Documentation
Per FDA requirements all Validation Packages/Turnover Packages include:
- Welder Certifications
- Material Certifications
- Purge gas certification
- Weld Logs
- Weld Maps
- Coupon Logs
- Electropolish and/or passivation certification
Project Efficiencies
- Constructability review and feedback process
- Reduce your risk on projects by bringing in the experts
Additional Services
- Pre-Fabrication
- Fabrication
- Tube Bending
- Pipe Bending
- Assembly
- On-Site/ Field Installation
- Prototyping
- Research and Development
- Embossing
- Etching
- Passivation
- Electropolishing
- Painting
- Powder Coating
- Polishing
- Testing
- CAD Drawing/Design Assistance/Layout and feasibility/Usability-Constructability Assistance
Additional Information
Industry Focus
- Semiconductor
- Microelectronics
- Biopharmaceutical
- Pharmaceutical
- Aerospace
- Medical/Medical Gas
- Hospital
- Pipeline
- Oil and Gas
- Petrochemical
- Research Laboratories
- Steam
- Brewery
- Food Processing
- Water Treatment
- Agricultural
- Automotive
- Marine
Typical Projects
- Process Systems
- Sanitary Spools
- Hygienic Spools
- High Purity Spools
- Carbon Steel Spools
- Stainless Steel Spools
- Vacuum Components
- Utility Panels
- Gas Delivery Systems
- Skidded Systems
- Dissimilar Metals Welds
- High Purity Clean Room Piping
Semiconductor Applications
- Process Tool Hook-up
- Orbital Welded Ultra High Purity (UHP) Grade Gas Systems
- DI-Water PVDF Systems, IR & SIB
- Double Containment Gas Systems
- Chemical and Waste Systems
- Process Tool Vacuum Systems
- Process Cooling Water Systems
- Base Build Laterals and Headers
- Fiber Optic Gas Systems
Biopharmaceutical Applications
- Clean Steam Systems
- RO Water Systems
- WFI Systems
- Validated Systems
- Lab Gases
- BioWaste Systems
- Custom Spool Piece Construction
- Utility Panels
- Transfer Panels
- J-Tubes
- Dip Tubes
- Valve Porting
- Bio-Reactor Skids
- Fermentation Skids
Aerospace Applications
- Gas Panels
- Purge Panels
- Vacuum Systems
- Cooling Systems
- Propulsion Weldment Assembly
- Thin wall tube bending of Titanium and Stainless Steel
- Hydraulic Lines
- Fueling Piping
- Cryogenic Piping
- Vacuum Systems
- Cooling Systems
- Process Piping Systems
- Custom Fabrication
Industry Standards Regularly Adhered To
- ASME B31.1 Power Piping
- ASME B31.3 Process Piping
- B31.3 Severe Cyclic Conditions where there is excessive displacement cycles in the piping system
- ASME B31.5 Refrigeration Piping and heat Transfer Components
- ASME B31.8 Gas Transmission and Distribution Piping Systems
- ASME B31.9 Building Services Piping
- API 1104 Welding of pipelines and Related Facilities
- AWS D1.1 Structural Welding Code – Steel
- AWS D1.2 Structural Welding Code – Aluminum
- AWS D1.3 Structural Welding Code – Sheet Steel
- AWS D1.4 Structural Welding Code – Reinforced Steel
- AWS D1.6 Structural Welding Code – Stainless Steel
- AWS D1.7 Guide for Strengthening and Repairing Existing Structures
- AWS D1.9 Structural Welding Code – Titanium
- AWS D18.1 Specification for Welding of Austenitic Stainless Steel Tube and Pipe Systems in Sanitary (Hygienic) Applications
- AWS D18.3 Specification for Welding of Tanks, Vessels, and Other Equipment in Sanitary (Hygienic) Applications
- Inspection per ASTM E1742
- Weld per AWS D17 1:2010
- Fabrication in accordance with cleaning spec IEST-STD-1246E
- PFI Standards
- Pipe & Fitting Manufacturer’s Installation Requirements
- FDA
Electronic File Formats
- SolidWorks (SLDPRT, SLDDRW, SLDDRT)
- AutoCAD (DWG)
- REVIT (RVT)
- NWC
- NWD
- DXF
- SAT
- STEP
- IGES
- 3DX
- PRT
- ASM
Contact High Purity Systems
Have a question about a piping challenge? Want to discuss an upcoming project? Let’s talk.